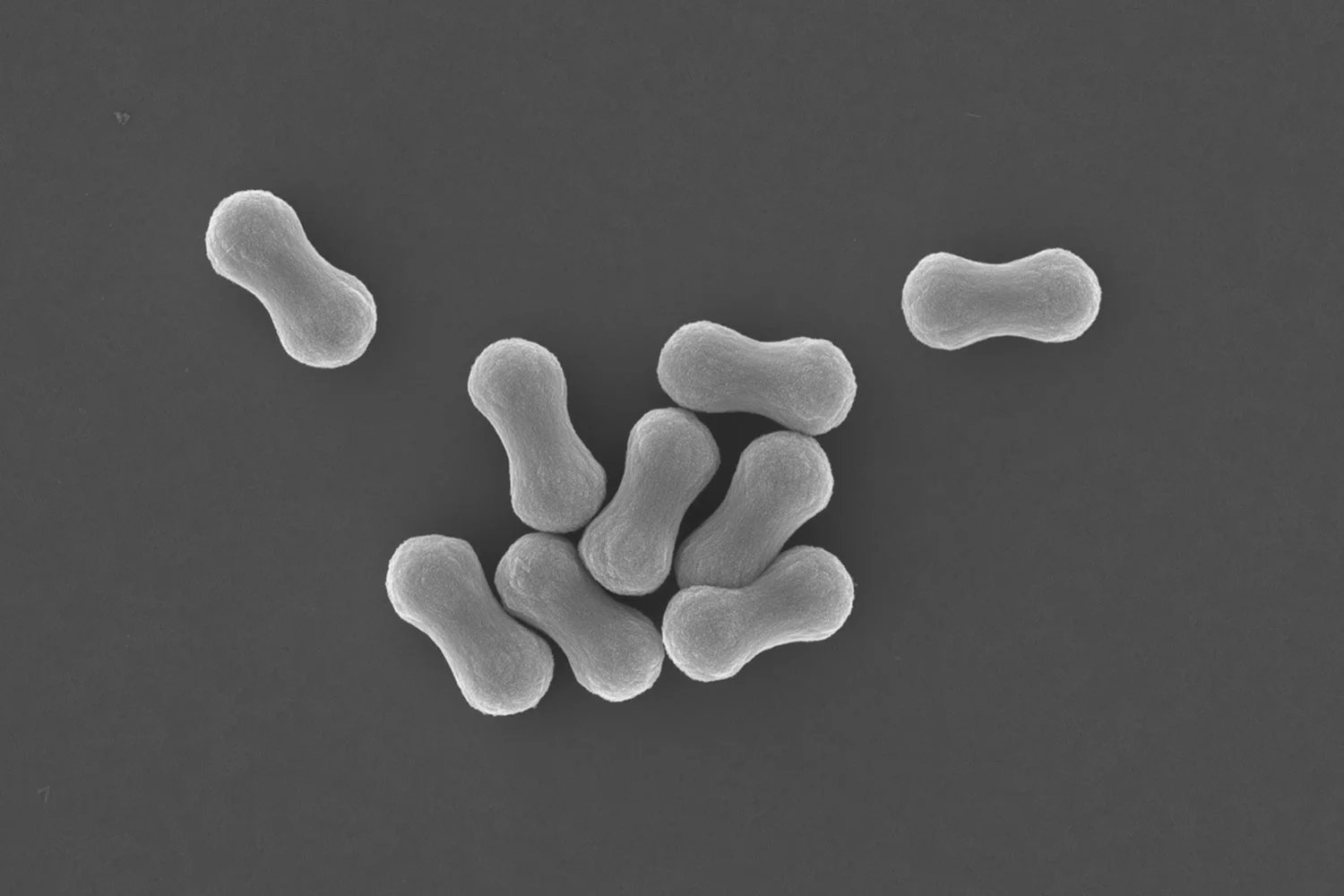
BONLAB BLOG
Thoughts
&
Scientific Fiction
Grafting polymers to graphene oxide goes better through branching
Single-layer graphene is interesting as a flexible 2D material, with xy-dimensions variable up to a centimetre in length and a z-thickness of a single carbon atom. It conducts heat and electricity, has excellent mechanical strength, and is impermeable to gases except hydrogen gas. Its drawback: how to disperse it in a liquid. When you try to do this flexible sheets of graphene tend to stack as a result of attractive van der Waals interactions, making it virtually an impossible material to disperse as single sheets.
Single-layer graphene is interesting as a flexible 2D material, with xy-dimensions variable up to a centimetre in length and a z-thickness of a single carbon atom. It conducts heat and electricity, has excellent mechanical strength, and is impermeable to gases except hydrogen gas. Its drawback: how to disperse it in a liquid. When you try to do this flexible sheets of graphene tend to stack as a result of attractive van der Waals interactions, making it virtually an impossible material to disperse as single sheets.
As a compromise, people came up with graphene oxide (GO), it’s oxidised analogue. The presence of oxygen atoms containing functional groups, such as hydroxy, epoxy, carboxylic acid, ketone, or aldehyde, provides it with a polarity, which makes it possible to disperse GO as single sheets in polar solvents, such as water or DMSO at low concentrations in the absence of electrolyte or other colloidal particles. The drawbacks: graphene oxide sheets have holes. Whereas graphene can be seen as a pristine, flexible bedsheet, graphene oxide is a bedsheet attacked by moths. This makes the material less suitable for barrier property reinforcement. Graphene oxide is also less electrically conducting as oxidation has partially destroyed its conjugation. Nevertheless, it still shows great potential for a range of applications, for example, those that need mechanical reinforcement, such as polymer nano-composites, but only if we can enhance its dispersibility in liquids or polymer melts.
Grafting polymer chains from the surface of GO allows it to be dispersed more easily. This can provide additional electrostatic and steric stabilization against sheet stacking at higher concentrations in less polar solvents or contain soluble polymer chains or non-interacting particles that can trigger depletion flocculation.
There are several approaches to accomplishing this, each with advantages and disadvantages. A particular challenge is linking a sufficient mass of polymer chains to the GO’s surface. In our gold open access paper recently published in the RSC journal Polymer Chemistry, we report a way to address this, employing radical polymerization reactions that lead to a branched polymer architecture. Methacrylate-based macromonomers made by catalytic chain transfer polymerization were used together as molecular weight regulators with dimethacrylates as crosslinkers to introduce branching points.
You can read the paper here:
BonLab designs a stick-on-demand adhesive for linerless labels
Labels are big business. A typical label has multiple layers: a topcoat for protection, the face stock, which contains the message in the form of text and/or images, a pressure-sensitive adhesive, and a release liner, which often has a release coating. The release liner and coating are only there to protect the label from sticking to things you do not wish it would stick to. You remove the liner when you wish to apply the label onto your substrate of choice, for example, a bottle containing a drink.
Imagine a label without a release liner and coating, imagine a label that could be activated at the moment you want it to stick to a substrate, a stick-on-demand linerless label.
BonLab has designed and developed a concept and prototype for a sustainable solution: a mesh reinforced pressure-sensitive adhesive for linerless label design.
Labels are big business. A typical label has multiple layers: a topcoat for protection, the face stock, which contains the message in the form of text and/or images, a pressure-sensitive adhesive, and a release liner, which often has a release coating. The release liner and coating are only there to protect the label from sticking to things you do not wish it would stick to. You remove the liner when you wish to apply the label onto your substrate of choice, for example, a bottle containing a drink.
Imagine a label without a release liner and coating, imagine a label that could be activated at the moment you want it to stick to a substrate, a stick-on-demand linerless label.
BonLab has designed and developed a concept and prototype for a sustainable solution: a mesh reinforced pressure-sensitive adhesive for linerless label design. The idea was worked out by Emily Brogden and prof. dr. ir. Stefan Bon, in collaboration with UPM Raflatac Oy, a global supplier of label materials for branding and promotion, information and functional labelling (patent application: WO2023105120A1). The complete study, which was done at the University of Warwick, is now published in the new journal RSC Applied Polymers.
A water-based pressure sensitive adhesive (PSA) is contained in a hard 3D mesh structure. This replaces the standard PSA layer of a label. It provides structural support upon storage and prevents the adhesive layer from sticking. In adhesive jargon: it shows excellent blocking resistance.
Upon short heat treatment, for example, upon contact with a hot sterilized glass bottle, the mesh will soften, allowing for adhesion to occur.
The 3D mesh structure was generated using a binary mixture of water-based polymer dispersions. One component is a standard PSA latex, and the other is a polystyrene polymer colloid. Film formation of the blend followed by a short annealing time led to the desired phase-separated mesh structure, as displayed in the figure below.
Visualization of the mesh structure in an acetone etched PVAc-PS model film (Film 1) a-c. a) SEM image of the top surface, b) a tilt adjusted image of the cross section after cutting away a section using FIB SEM with a film height of approximately 20 𝜇𝑚, and c) micro-CT 3D reconstruction of the etched film. Visualization of a similar mesh structure in a PSA-PS film (Film 2) d-f. d) SEM image of the top surface of Film 2, annealed for 60 𝑚𝑖𝑛 e) SEM image of the top surface (prepared similiarly to Film 2 but with only a 19 𝑚𝑖𝑛 annealing time) with a clean crack after freezing in liquid nitrogen and f) a cross section of Film 2, where the PS is tagged with hostasol methacrylate (green), taken using confocal microscopy (the original top surface of the cast film is at the top of the image).
Prof. dr. ir. Stefan Bon says: “I am immensely proud of the hard work done by all people involved to get the idea from a sketch on a piece of paper to a working prototype. A big thank you to PhD researcher Emily Brodgen, the paper's first author, who has been the driving force behind turning a concept into reality and has worked tremendously hard on the project for the last couple of years. The work has received excellent feedback from the academic and industrial scientific communities, with Emily winning multiple prizes for best talk and scientific poster.”
The paper can be accessed from the RSC Applied Polymers website:
https://doi.org/10.1039/D3LP00224A
A promotional video will be made available soon.
Use of macromonomers as reactive stabilizers in mini-emulsion polymerization
A mini-emulsion polymerization is a variation on the more conventional emulsion polymerization process in that in the ideal scenario latex particles are formed by monomer droplet nucleation. The monomer droplets are turned into polymer particles. The trick to achieve this is to shrink monomer emulsion droplets to sub-micrometer diameters. For this two ingredients are key, one is a lyophobe, a compound that dissolves in the monomer droplet but does not like to partition into the continuous phase, here water. Typically n-hexadecane is used. This compound suppresses coarsening, also called Ostwald ripening, of the droplets by providing an Osmotic counter pressure. The other essential ingredient is a surfactant which aids to stabilize the large combined surface area of the droplets and keeps then from colliding and fusing (colloidal stability).
The use of molecular surfactants, however, can have negative impacts when the polymer latex is used in formulations and applications as the surfactant can migrate. For example in a clear coating it could lead to uptake of water, causing the transparent coating to become opaque, a phenomenon known as water whitening.
A mini-emulsion polymerization is a variation on the more conventional emulsion polymerization process in that in the ideal scenario latex particles are formed by monomer droplet nucleation. The monomer droplets are turned into polymer particles. The trick to achieve this is to shrink monomer emulsion droplets to sub-micrometer diameters. For this two ingredients are key, one is a lyophobe, a compound that dissolves in the monomer droplet but does not like to partition into the continuous phase, here water. Typically n-hexadecane is used. This compound suppresses coarsening, also called Ostwald ripening, of the droplets by providing an Osmotic counter pressure. The other essential ingredient is a surfactant which aids to stabilize the large combined surface area of the droplets and keeps then from colliding and fusing (colloidal stability).
The use of molecular surfactants, however, can have negative impacts when the polymer latex is used in formulations and applications as the surfactant can migrate. For example in a clear coating it could lead to uptake of water, causing the transparent coating to become opaque, a phenomenon known as water whitening.
Already in the 1990s one came up with the solution to use surfactants that could become part of the polymer. Buzzwords were inisurfs, surfmers, and transsurfs.
In our paper we look at macromonomers that are surfactants, which have been made by a technique called catalytic chain transfer emulsion polymerization (see image for chemical structure), and use these as reactive stabilizers in mini-emulsion polymerization.
ω-Unsaturated methacrylate macromonomers as reactive polymeric stabilizers in mini-emulsion polymerization
These macromonomers are of renewed interest, and indeed we have used them in bonlab before to demonstrate polymerization induced self-assembly (PISA), their modification into reactive nanogels as Pickering stabilizers to make Janus and patchy polymer colloids, and as stabilizers in conventional emulsion polymerization.
The paper focusses on a mechanistic study on how they operate as colloidal stabilizers and what the impact of their use is on the mini-emulsion polymerization process with a focus on particle size distribution and morphology. PhD researchers Josh Booth and Josh Davies (an undergraduate student at the time) carried out the experimental work which formed the basis of this study.
We believe there is evidence that polymerization triggers a destabilization of the balance between Ostwald ripening and the added hexadecane hydrophobe, evident from particle shape analysis. Also we show that too much surfactant is bad, as it can trigger depletion flocculation on the mini-emulsion droplets during high-shear emulsification.
The paper is published in the scientific journal Polymer Chemistry from the Royal Society of Chemistry.
More on the paper: