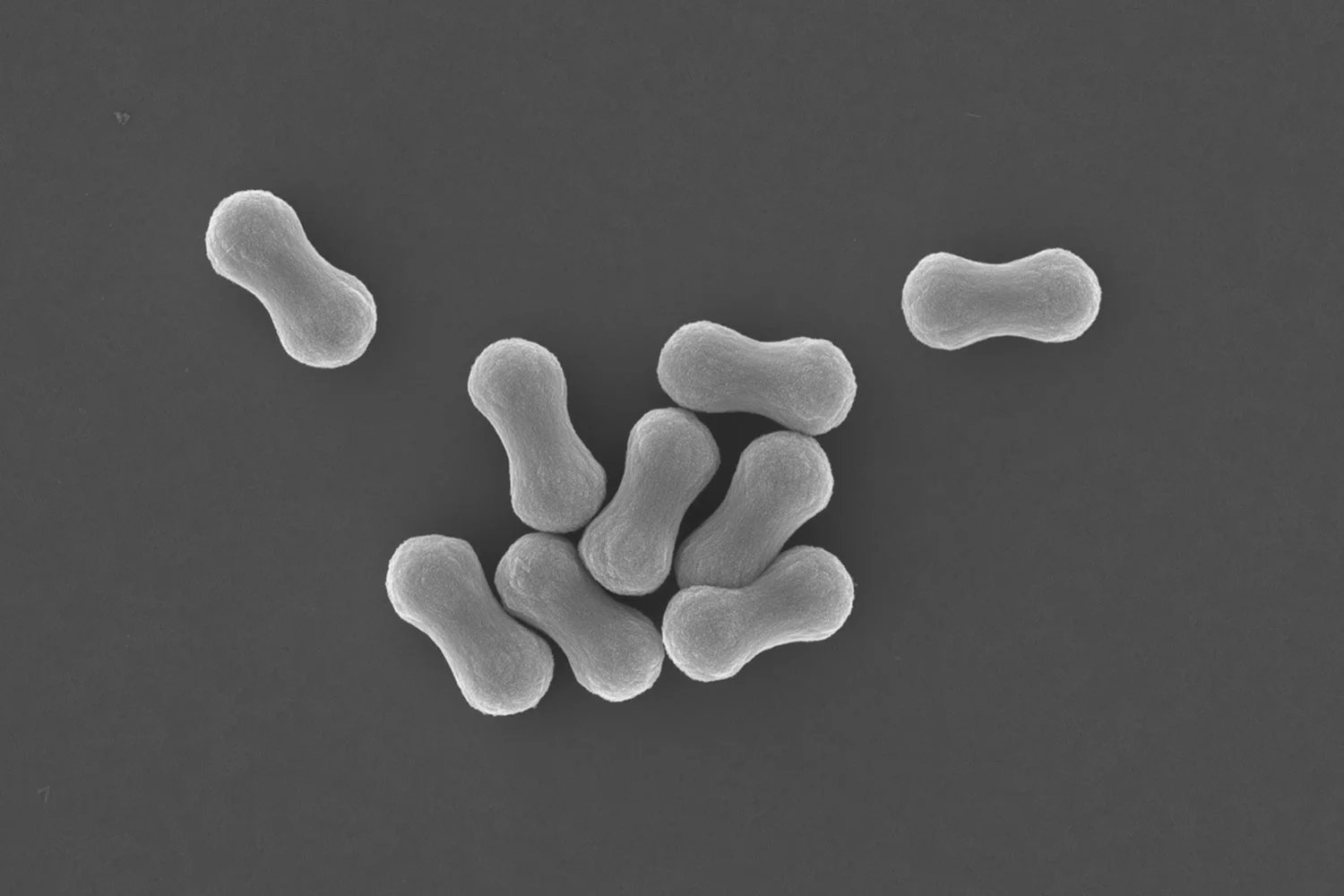
BONLAB BLOG
Thoughts
&
Scientific Fiction
Warwick drives green growth with £13.6M EPSRC hub in plastics
From developing greener materials and processes to growing more sustainable supply chains, a new £13.6 million research hub, funded by the Engineering and Physical Sciences Research Council (EPSRC), will help researchers at the University of Warwick tackle some of the UK’s biggest manufacturing challenges.
The new Manufacturing Research Hub in Sustainable Engineering Plastics (SEP) will be led by Professor of Polymer Processes, Ton Peijs, at WMG, and has Professor of Polymer and Colloid Chemical Engineering, Stefan Bon, at the Department of Chemistry as one of the co-investigators.
From developing greener materials and processes to growing more sustainable supply chains, a new £13.6 million research hub, funded by the Engineering and Physical Sciences Research Council (EPSRC), will help researchers at the University of Warwick tackle some of the UK’s biggest manufacturing challenges.
The new Manufacturing Research Hub in Sustainable Engineering Plastics (SEP) will be led by Professor of Polymer Processes, Ton Peijs, at WMG, and has Professor of Polymer and Colloid Chemical Engineering, Stefan Bon, at the Department of Chemistry as one of the co-investigators.
Researchers from Warwick will work, over the next seven years, alongside the University of Manchester and UCL to improve the way durable plastics – commonly used in cars, buildings, and electronics – are created, reused, and recycled. Researchers aim to reduce waste, support greener manufacturing practices, and advance the circular economy, with support from over 60 industry partners, including JLR, Polestar, Siemens, BEKO, Bellway, and Biffa, to turn research into real-world solutions.
By focusing on practical needs, the Hub will help move the UK toward a circular economy—where products are reused instead of thrown away. The work will support businesses in reducing waste and minimizing their environmental impact, while maintaining competitiveness. It will also strengthen local supply chains and help shape future policies that promote innovation and sustainability in the UK manufacturing sector.
Professor Ton Peijs, Project Lead, of the EPSRC Manufacturing Research Hub in Sustainable Engineering Plastics, said: “We’re incredibly proud to lead this vital initiative. Until now, most sustainability efforts in plastics have focused on single-use items and packaging. Yet engineering plastics - essential to modern life - present equally complex sustainability challenges that have, until now, largely been overlooked.
This Hub unites researchers, industry leaders, and policymakers to fundamentally rethink how engineering plastic parts are designed, reused, repaired and recycled. We’re focused on real-world impact: using greener materials, smarter manufacturing and recycling systems, and more sustainable supply chains.
This grant underscores the urgent need for innovation in this space, and we’re excited to drive meaningful, lasting change.”
Professor Stefan Bon, co-investigator, from the Department of Chemistry says: “We at Warwick, the University of Manchester, and UCL worked tremendously hard to get this initiative over the line. It is good to see that the UK government recognises the value of its polymer science and engineering capabilities. The next 7-8 years will be fantastic!”
The Hub is one of four, backed by a total of £44 million through the EPSRC the new Manufacturing Research Hubs for a Sustainable Future will bring together world-class researchers with over 180 industry and civic partners to drive practical, sustainable innovation across the UK.
Each hub will focus on a different critical area of manufacturing, including creating net-zero supply chains and resilient production systems, as well as transforming waste and reducing our reliance on fossil fuels.
Professor Charlotte Deane, Executive Chair of EPSRC, said: “These hubs will play a vital role in reshaping manufacturing to help the UK achieve green growth. By combining deep research expertise with real-world partnerships, they will develop the technologies, tools, and systems we need for clean, competitive, and resilient industries.”
For more info see UKRI: https://www.ukri.org/news/new-research-hubs-to-cut-carbon-and-reshape-uk-manufacturing/
Warwick Researchers Lead the Way in Developing Sustainable Alternatives to Plastics
Researchers at The University of Warwick have made significant progress in the search for sustainable alternatives to conventional plastics. In response to growing environmental concerns, the move towards a circular economy and changing consumer preferences, the research team has identified that certain mixtures of small organic molecules form interesting glasses and viscous liquids. These so-called organic eutectics are promising candidates for replacing polymers in various products.
Researchers at The University of Warwick have made significant progress in the search for sustainable alternatives to conventional plastics. In response to growing environmental concerns, the move towards a circular economy and changing consumer preferences, the research team has identified that certain mixtures of small organic molecules form interesting glasses and viscous liquids. These so-called organic eutectics are promising candidates for replacing polymers in various products.
Plastics have long been a mainstay in modern manufacturing, but their environmental impact has increased demand for eco-friendly alternatives. The Warwick research highlights eutectic molecular glasses and liquids—materials formed by mixing crystalline components—as underexplored yet highly promising options for this purpose.
The team successfully developed a series of hydrophobic eutectic molecular liquids and glasses, each carefully crafted by combining different crystalline components. Using advanced techniques like differential scanning calorimetry (DSC) and UV-vis spectroscopy, the eutectic compositions were precisely determined. The analysis was refined using a trained partial least squares regression model, ensuring accuracy in identifying the optimal material blends.
Fibers can be pulled from the hydrophobic small-molecule eutectic material. It can also be molded into shapes, glass-blown into baubles, or cast as flexible films.
One key challenge in creating sustainable plastic alternatives is ensuring long-term stability. The Warwick team addressed this by testing the amorphous materials over an extended period of up to 14 months, using powder X-ray diffraction (PXRD) to confirm their resistance to crystallization. This durability is crucial for ensuring that products maintain their integrity throughout their shelf life.
In addition to stability, the researchers investigated the processability of these materials by examining their rheological properties. They found that all the liquids exhibited low fragility indices, making them suitable for various manufacturing processes, including glassblowing, fiber pulling, film formation, and molding. Importantly, the team demonstrated that the properties of these materials could be tailored to specific applications by blending different eutectic systems or incorporating plasticizers.
Prof. dr. ir. Stefan Bon, lead investigator of the work, says: “The original plan was to develop an anything-but-plastic concept material for the formulation industry. Dr. Joshua Ryan, a talented former PhD researcher in my team, BonLab, undertook a systematic study of blending small hydrophobic organic molecules that could undergo a variety of non-covalent interactions with one another. That these hydrophobic eutectic systems had such remarkable physical properties, was beyond our initial expectations. We brought our colleague Prof. Gabriele Sosso on board to study by computer simulations how these eutectic mixtures interacted on a molecular level. These small molecule organic eutectic systems offer an opportunity to further develop high-performance materials that can replace conventional polymers in various applications. In a way, they can be seen as a non-covalent analogue to dynamic reversible macromolecular covalent materials, known as vitrimers.”
To showcase the practical potential of these materials, the researchers conducted a controlled release study using a eutectic system composed of 4-hydroxychalcone and bifonazole as a matrix. This study serves as a proof-of-concept, highlighting the versatility of eutectic materials in applications such as drug delivery and beyond.
The University of Warwick's groundbreaking research, published open access in Chemical Science, the flagship journal of the Royal Society of Chemistry, opens new avenues for developing sustainable, versatile alternatives to traditional plastics. As legislative changes and consumer preferences continue to push for greener solutions, these innovative organic materials offer a promising path forward.
ENDS
The scientific paper entitled “Small molecule organic eutectics as candidates to replace plastics.” published in Chemical Science can be accessed at: https://doi.org/10.1039/D4SC02574A
For more information on BonLab, see https://bonlab.info
For more information, please contact the University of Warwick press office at press@warwick.ac.uk or phone 07392 125 605
Water-Based Acrylic Latexes are excellent Pressure Sensitive Adhesives when Branched
Water-based pressure sensitive adhesives (PSAs) are typically made by emulsion polymerization using a low glass transition temperature base monomer, such as n-butyl acrylate or 2-ethyl hexylacrylate, together with a range of functional comonomers. Typically these include a high glass transition temperature comonomer, such as styrene or methyl methacrylate and monomers that can promote wetting and undergo secondary interactions such as (meth)acrylic acid.
Water-based pressure sensitive adhesives (PSAs) are typically made by emulsion polymerization using a low glass transition temperature base monomer, such as n-butyl acrylate or 2-ethyl hexylacrylate, together with a range of functional comonomers. Typically these include a high glass transition temperature comonomer, such as styrene or methyl methacrylate and monomers that can promote wetting and undergo secondary interactions such as (meth)acrylic acid.
A golden rule for good adhesive performance is that the polymer latex particles must contain a certain fraction of gel, that is, cross-linked material. This typically is 50-70%. This gel content optimizes the balance between tack and cohesive forces within the adhesive.
Schematic of the branched polymer chain architecture approach to deliver good performance in pressure sensitive adhesives (PSAs).
In our paper, led by PhD researcher Emily Brogden and published in the RSC journal Polymer Chemistry, we challenged this view. Prof. dr. ir. Stefan Bon says: “We designed a range of polymer latexes with low gel content. To balance the adhesive forces, we introduced a branched polymer chain architecture instead. We show that excellent water-based acrylic PSAs can be made using this approach.”
Moreover, the chemical composition of our PSA was designed with sustainability in mind. The base monomer selected was the bio-based 2-octyl acrylate, the high Tg component bio-based 2-isobornyl acrylate. The other monomers and chain transfer agent show promise to be or become fully bio-based.
The paper entitled “Water-Based Polymer Colloids with a Branched Chain Architecture as Low-Gel Pressure-Sensitive Adhesives” has gold open access and can be read here: