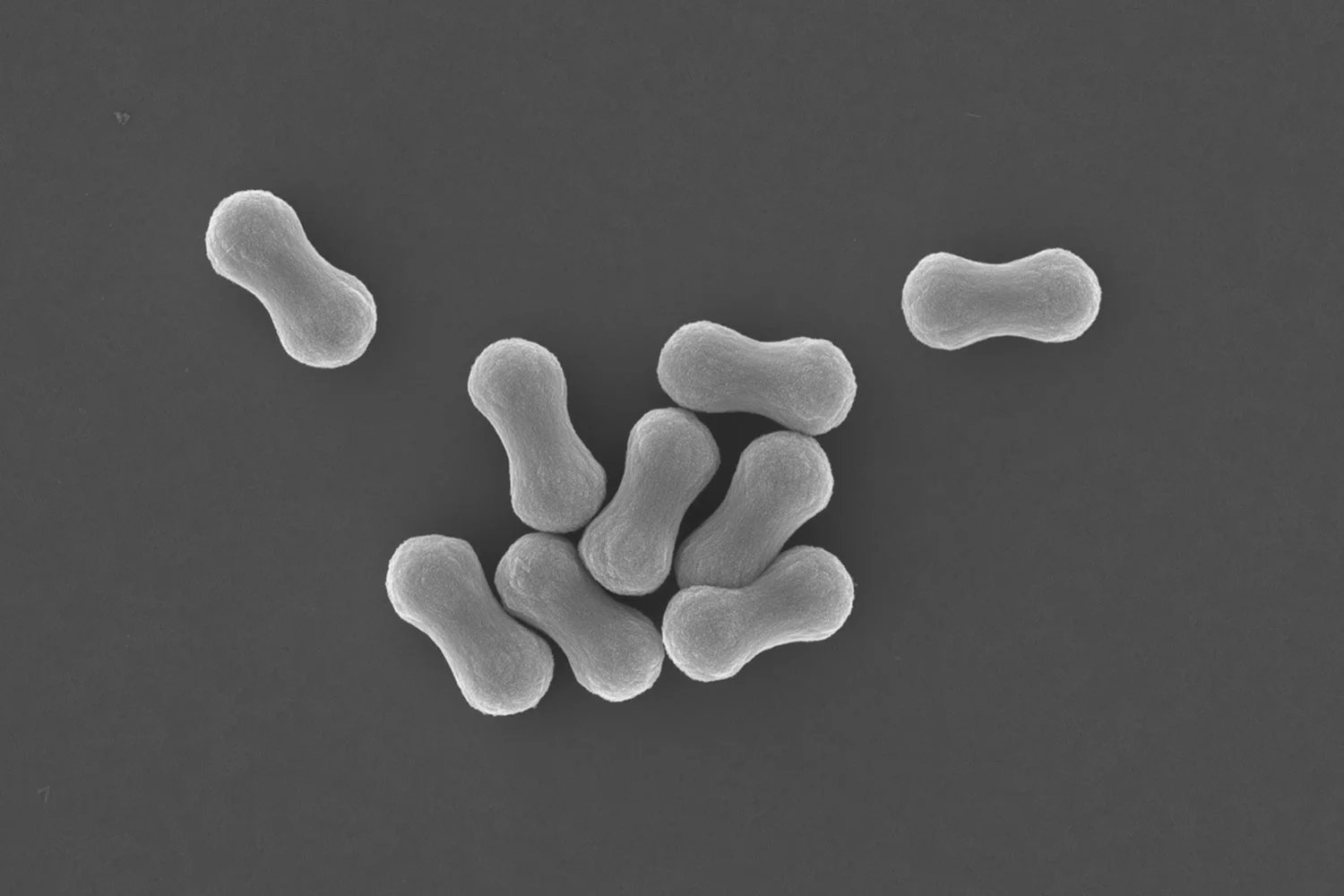
BONLAB BLOG
Thoughts
&
Scientific Fiction
Templating Calcium Phosphate onto Graphene Oxide Sheets
Single-layer graphene oxide sheets are interesting as a flexible 2D material, with xy-dimensions variable up to a centimetre in length and a z-thickness of a single carbon atom. The presence of oxygen atoms with functional groups, such as hydroxy, epoxy, carboxylic acid, ketone, or aldehyde, provides graphene oxide (GO) with polarity. This unique property allows GO to disperse as single sheets in polar solvents like water or DMSO at low concentrations, in the absence of electrolytes or other colloidal particles.
Single-layer graphene oxide sheets are interesting as a flexible 2D material, with xy-dimensions variable up to a centimetre in length and a z-thickness of a single carbon atom. The presence of oxygen atoms with functional groups, such as hydroxy, epoxy, carboxylic acid, ketone, or aldehyde, provides graphene oxide (GO) with polarity. This unique property allows GO to disperse as single sheets in polar solvents like water or DMSO at low concentrations, in the absence of electrolytes or other colloidal particles.
Our recent findings, published in RSC Polymer Chemistry (https://doi.org/10.1039/D4PY00300D), have shown that grafting polymer chains from the surface of GO significantly enhances its dispersion. This is particularly true when the polymer chains are of a branched chain architecture. The grafted branched polymer chains provide additional electrostatic and steric stabilization against sheet stacking and crumpling, a discovery that could have significant implications in the field of materials science.
SEM images of single graphene oxide sheets that are decorated with a layer of calcium phosphate, deposited to a templated synthesis route.
The 2D architecture of single GO sheets dispersed in water is an exciting template for depositing inorganic materials, especially now that the grafted polymer chains can be engineered to withstand the ionic precursor concentrations so that the sheets remain dispersed and can additionally serve as crystal nucleation sites.
In our paper published in the Journal of Colloid and Interface Science we show that it is possible to grow Calcium Phosphate onto single dispersed sheets of GO in water. The work was led by former PhD researcher dr. Wai Hin Lee.
Prof. dr. ir. Stefan Bon says: “This paper shows that as a result of the grafted branched polymer, the use of dispersed Graphene Oxide sheets as a template for mineralization is now possible and straightforward. It opens up all sorts of possibilities for hybrid material design”
You can read the paper here: https://doi.org/10.1016/j.jcis.2024.06.221
What happens to particle size distributions when making reactive surfactants and polymer colloids by emulsion polymerization?
When we synthesize polymer colloids by emulsion polymerization, molecular surfactants are often employed. These are required to keep the polymer latex particles dispersed in the water phase, so that they do not clump together, a phenomenon known as coagulation. Keeping polymer dispersions stable is especially important in end applications, such as waterborne coatings and adhesives.
A downside of the use of surfactant molecules is that they can desorb from the surface of the latex particles. This makes the particles colloidally unstable, and they coagulate. This can be disastrous in product formulations, such as water-based paints which have many components. Another downside of this mobility of the surfactant molecules is that they can migrate in the final coating, once applied on a substrate. This leads to deterioration of the properties of the coated film.
When we synthesize polymer colloids by emulsion polymerization, molecular surfactants are often employed. These are required to keep the polymer latex particles dispersed in the water phase, so that they do not clump together, a phenomenon known as coagulation. Keeping polymer dispersions stable is especially important in end applications, such as waterborne coatings and adhesives.
A downside of the use of surfactant molecules is that they can desorb from the surface of the latex particles. This makes the particles colloidally unstable, and they coagulate. This can be disastrous in product formulations, such as water-based paints which have many components. Another downside of this mobility of the surfactant molecules is that they can migrate in the final coating, once applied on a substrate. This leads to deterioration of the properties of the coated film.
A solution to these problems is to use reactive surfactants. These have the ability to attach themselves to the latex particles irreversibly, through a covalent chemical bond.
Catalytic chain transfer polymerization (CCTP), a free radical polymerization processs that employs a cobalt catalyst in tiny amounts, is able to make polymer molecules with a reactive unsaturated end group. These macromolecules, also called macromonomers, can be chain extended using a process referred to as RAFT (Reversible Addition Fragmentation chain Transfer), into longer polymer molecules that can behave like surfactant molecules. The reactive end group is preserved, which means that if our polymer reactive surfactant is used in an emulsion polymerization to make latex particles, it will be attached permanently to the latex particles.
The technology to fabricate blockcopolymers under emulsion polymerization conditions using CCTP derived macromonomers, was originally reported in the 1990s by Moad and coworkers. Emphasis has been lying on polymer chain growth and hence the molecular weight distribution.
In our paper published in a special polymer colloids issue of the ACS journal Biomacromolecules PhD students Wai Hin Lee and Joshua Booth investigated the emulsion polymerization processes from a different angle. We investigated the particle size distributions and studied how these developed throughout a three-stage emulsion polymerization process (see the image below).
Three stages of emulsion polymerizations: Catalytic chain transfer emulsion polymerization to make an alkali soluble macromonomer, chain extension to make a reactive block copolymer surfactant, emulsion polymerization to prepare soft polymer colloids using the reactive surfactant.
Firstly, we looked at the catalytic chain transfer emulsion polymerization to make the hydrophilic block of the reactive polymer surfactants. Next we looked at how the particle size distributions changed upon chain extension with a hydrophobic block. Finally, we disintegrated the latex particles into a reactive polymer surfactant micellar dispersion. This was then used to carry out emulsion polymerizations to produce polymer latexes in absence of conventional surfactants.
Prof. dr. ir. Stefan Bon says: “I hope that people like the angle we took in our work, to shine a light on how the latex particles are formed and how the particle size distributions develop. We showed that it was possible to make soft polymer latexes with average particle diameters below 100 nm using our reactive surfactants, easily up to overall solids content of 30wt%. This is an excellent achievement. We believe that the reported emulsion polymerization processes are robust and versatile, and are delighted that we can produce polymer latexes that do not suffer from surfactant migration upon application.”
Details on the paper : https://pubs.acs.org/doi/10.1021/acs.biomac.0c00766
Innovation in Emulsion Polymerization process opens window to Janus and patchy particles
Emulsion polymerization is of pivotal importance as a route to the fabrication of water-based synthetic polymer colloids. The product is often referred to as a polymer latex and plays a crucial role in a wide variety of applications spanning coatings (protective/decorative/automotive), adhesives (pressure sensitive/laminating/construction), paper and inks, gloves and condoms, carpets, non-wovens, leather, asphalt paving, redispersible powders, and as plastic material modifiers.
Since its discovery in the 1920s the emulsion polymerization process and its mechanistic understanding has evolved. Our most noticeable past contributions include the first reversible-deactivation nitroxide-mediated radical emulsion polymerization (Macromolecules 1997: DOI 10.1021/ma961003s), and the development and mechanistic understanding of Pickering mini-emulsion (Macromolecules 2005: DOI 10.1021/ma051070z) and emulsion polymerization processes (J. Am. Chem. Soc. 2008: DOI 10.1021/ja807242k). The latest on nano-silica stabilized Pickering Emulsion Polymerization from our lab can be found here.
One quest in emulsion polymerization technology that remains challenging and intriguing is control of the particle morphology. It is of importance as the architecture of the polymer colloid influences its behavioural properties when used in applications. We now report in ACS Nano an elegant innovation in the emulsion polymerization process which makes use of nanogels as stabilizers and allows us to fabricate Janus and patchy polymer colloids.
Emulsion polymerization is of pivotal importance as a route to the fabrication of water-based synthetic polymer colloids. The product is often referred to as a polymer latex and plays a crucial role in a wide variety of applications spanning coatings (protective/decorative/automotive), adhesives (pressure sensitive/laminating/construction), paper and inks, gloves and condoms, carpets, non-wovens, leather, asphalt paving, redispersible powders, and as plastic material modifiers.
Since its discovery in the 1920s the emulsion polymerization process and its mechanistic understanding has evolved. Our most noticeable past contributions include the first reversible-deactivation nitroxide-mediated radical emulsion polymerization (Macromolecules 1997: DOI 10.1021/ma961003s), and the development and mechanistic understanding of Pickering mini-emulsion (Macromolecules 2005: DOI 10.1021/ma051070z) and emulsion polymerization processes (J. Am. Chem. Soc. 2008: DOI 10.1021/ja807242k). The latest on nano-silica stabilized Pickering Emulsion Polymerization from our lab can be found here.
One quest in emulsion polymerization technology that remains challenging and intriguing is control of the particle morphology. It is of importance as the architecture of the polymer colloid influences its behavioural properties when used in applications. We now report in ACS Nano an elegant innovation in the emulsion polymerization process which makes use of nanogels as stabilizers and allows us to fabricate Janus and patchy polymer colloids.
False coloured SEM images of emulsion polymerizations using nanogels as stabilizers (N1) at 2.8 wt% wrt monomer in which the pH was adjusted to 8.8 (A), 5.5 (B), 5.0 (C) and 4.5 (D) prior to polymerization. Scale bars: 100 nm.
The use of the nanogels in the emulsion polymerization leads to anisotropic Janus and patchy colloids, where a latex particle is decorated with a number of patches on its surface. In the paper we show that control of particle size and patch density can be achieved by tailoring the reaction conditions.
Proposed mechanism for the formation of Janus and patchy particles in the emulsion polymerization of styrene carried out in presence of nanogel particles.
The work was carried out by a team of talented scientists from the BonLab, Andrea Lotierzo, Brooke Longbottom, and Wai Hin Lee. Prof.dr.ir. Stefan Bon says: “ I am absolutely delighted that our work is published in the internationally leading journal ACS Nano. It is a great achievement of the team who have worked tremendously hard in the realisation of this new innovative technology. It shows that the area of emulsion polymerization is very much alive and kicking!”
The link to the paper is here: DOI: 10.1021/acsnano.8b06557