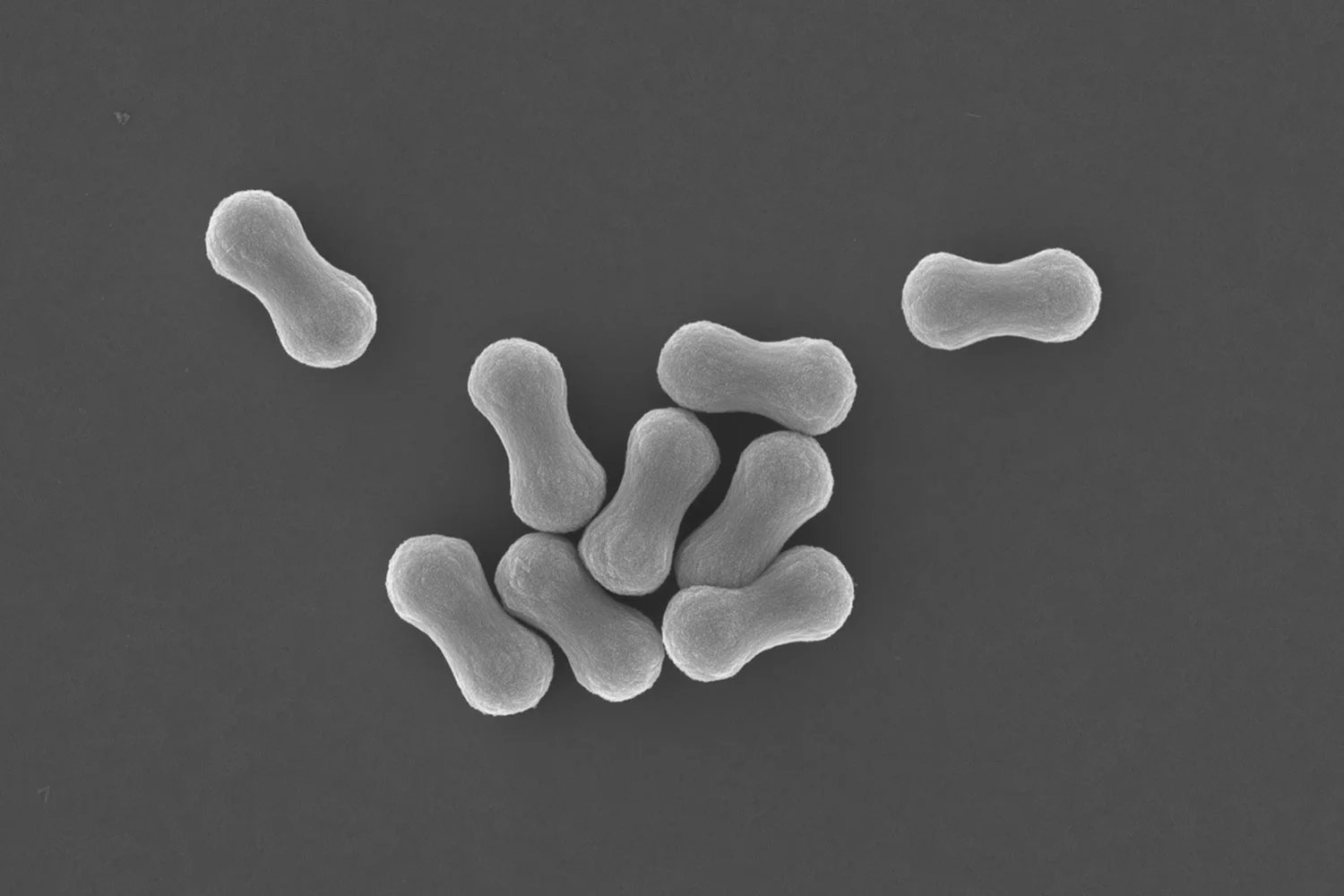
BONLAB BLOG
Thoughts
&
Scientific Fiction
Use of macromonomers as reactive stabilizers in mini-emulsion polymerization
A mini-emulsion polymerization is a variation on the more conventional emulsion polymerization process in that in the ideal scenario latex particles are formed by monomer droplet nucleation. The monomer droplets are turned into polymer particles. The trick to achieve this is to shrink monomer emulsion droplets to sub-micrometer diameters. For this two ingredients are key, one is a lyophobe, a compound that dissolves in the monomer droplet but does not like to partition into the continuous phase, here water. Typically n-hexadecane is used. This compound suppresses coarsening, also called Ostwald ripening, of the droplets by providing an Osmotic counter pressure. The other essential ingredient is a surfactant which aids to stabilize the large combined surface area of the droplets and keeps then from colliding and fusing (colloidal stability).
The use of molecular surfactants, however, can have negative impacts when the polymer latex is used in formulations and applications as the surfactant can migrate. For example in a clear coating it could lead to uptake of water, causing the transparent coating to become opaque, a phenomenon known as water whitening.
A mini-emulsion polymerization is a variation on the more conventional emulsion polymerization process in that in the ideal scenario latex particles are formed by monomer droplet nucleation. The monomer droplets are turned into polymer particles. The trick to achieve this is to shrink monomer emulsion droplets to sub-micrometer diameters. For this two ingredients are key, one is a lyophobe, a compound that dissolves in the monomer droplet but does not like to partition into the continuous phase, here water. Typically n-hexadecane is used. This compound suppresses coarsening, also called Ostwald ripening, of the droplets by providing an Osmotic counter pressure. The other essential ingredient is a surfactant which aids to stabilize the large combined surface area of the droplets and keeps then from colliding and fusing (colloidal stability).
The use of molecular surfactants, however, can have negative impacts when the polymer latex is used in formulations and applications as the surfactant can migrate. For example in a clear coating it could lead to uptake of water, causing the transparent coating to become opaque, a phenomenon known as water whitening.
Already in the 1990s one came up with the solution to use surfactants that could become part of the polymer. Buzzwords were inisurfs, surfmers, and transsurfs.
In our paper we look at macromonomers that are surfactants, which have been made by a technique called catalytic chain transfer emulsion polymerization (see image for chemical structure), and use these as reactive stabilizers in mini-emulsion polymerization.
ω-Unsaturated methacrylate macromonomers as reactive polymeric stabilizers in mini-emulsion polymerization
These macromonomers are of renewed interest, and indeed we have used them in bonlab before to demonstrate polymerization induced self-assembly (PISA), their modification into reactive nanogels as Pickering stabilizers to make Janus and patchy polymer colloids, and as stabilizers in conventional emulsion polymerization.
The paper focusses on a mechanistic study on how they operate as colloidal stabilizers and what the impact of their use is on the mini-emulsion polymerization process with a focus on particle size distribution and morphology. PhD researchers Josh Booth and Josh Davies (an undergraduate student at the time) carried out the experimental work which formed the basis of this study.
We believe there is evidence that polymerization triggers a destabilization of the balance between Ostwald ripening and the added hexadecane hydrophobe, evident from particle shape analysis. Also we show that too much surfactant is bad, as it can trigger depletion flocculation on the mini-emulsion droplets during high-shear emulsification.
The paper is published in the scientific journal Polymer Chemistry from the Royal Society of Chemistry.
More on the paper:
Autonomous electricity-free "icy road" warning signs
We set out to develop a prototype for “icy road” warning signs which was able to operate autonomously without the use of electricity, and which could be easily placed onto existing road features, such as street boundary pillars and road safety barriers.
The number of road accidents in the UK under frosty or icy conditions runs in the thousands. Our concept would aid to reduce these numbers, without the introduction of a digital, and thus electric, infrastructure.
The results from our studies are now published open access in the Journal of Materials Chemistry C from the Royal Society of Chemistry. The conceptual road sign application is a multi-lamellar flexible strip.
We set out to develop a prototype for “icy road” warning signs which was able to operate autonomously without the use of electricity, and which could be easily placed onto existing road features, such as street boundary pillars and road safety barriers.
The number of road accidents in the UK under frosty or icy conditions runs in the thousands. Our concept would aid to reduce these numbers, without the introduction of a digital, and thus electric, infrastructure.
The results from our studies are now published open access in the Journal of Materials Chemistry C from the Royal Society of Chemistry. The conceptual road sign application is a multi-lamellar flexible strip.
A temperature triggered response in the form of an upper critical solution temperature (UCST) type phase separation targeted near the freezing point of water manifests itself through light scattering as a clear-to-opaque transition. It is simultaneously amplified by an enhanced photoluminescence effect. The essence is summed up in the supporting video.
The active layer in the strip is a polystyrene-based solution. When the temperature drops to near freezing the polymer molecules undergo a phase transition, from a coil happily dissolved, into a globule that crashes out of solution. This crashing out (phase separation) triggers the transparent active layer to become cloudy white, and thus opaque. The temperature at which this occurs is referred to as the cloud point. It is the result of the scattering of light caused by the different refractive indices of the two phases.
The clear-to-opaque transition of the active layer on the black strip allows us to introduce colour, either by adding a dye dissolved in the plasticizer liquid, or by printing a coloured translucent image on the top layer of the strip. This effect is shown in the image below where Pac-Man’s ghost only appear under freezing conditions.
Road sign displaying full colour temperature response by adding oil blue, rose bengal, and 4-phenylazopheonl dyes to polystyrene-DOP mixture. The patch was imaged at below, above and below phase separation temperature (freezing point of water), top, middle and bottom, respectively.
We wanted our road sign to be more visible in the dark. For this the concept of restricted motion enhanced photoluminescence, often referred to as aggregation-induced emission (AIE), was used. Polystyrene labelled with tetraphenylethylene (TPE) was used for this. The fluorescent tag emits light vividly under icy conditions, as the combination of phase separation, increased viscosity of the system, and lower temperatures restricts its motion and thus enhances its light emission (see video).
Prof. dr. ir. Stefan Bon says: “We worked on this project for a number of years, with a team of talented people which included undergraduate, master, and PhD students and research fellows. The project was co-led by Robert Young and Joshua Booth, who are shared first author on the paper. We are delighted with how it turned out, and are pleased that all is now published open access in the Journal of Materials Chemistry C. We hope that people are enthusiastic about the concept.”
The paper can be accessed from here:
https://doi.org/10.1039/D1TC01189H
What happens to particle size distributions when making reactive surfactants and polymer colloids by emulsion polymerization?
When we synthesize polymer colloids by emulsion polymerization, molecular surfactants are often employed. These are required to keep the polymer latex particles dispersed in the water phase, so that they do not clump together, a phenomenon known as coagulation. Keeping polymer dispersions stable is especially important in end applications, such as waterborne coatings and adhesives.
A downside of the use of surfactant molecules is that they can desorb from the surface of the latex particles. This makes the particles colloidally unstable, and they coagulate. This can be disastrous in product formulations, such as water-based paints which have many components. Another downside of this mobility of the surfactant molecules is that they can migrate in the final coating, once applied on a substrate. This leads to deterioration of the properties of the coated film.
When we synthesize polymer colloids by emulsion polymerization, molecular surfactants are often employed. These are required to keep the polymer latex particles dispersed in the water phase, so that they do not clump together, a phenomenon known as coagulation. Keeping polymer dispersions stable is especially important in end applications, such as waterborne coatings and adhesives.
A downside of the use of surfactant molecules is that they can desorb from the surface of the latex particles. This makes the particles colloidally unstable, and they coagulate. This can be disastrous in product formulations, such as water-based paints which have many components. Another downside of this mobility of the surfactant molecules is that they can migrate in the final coating, once applied on a substrate. This leads to deterioration of the properties of the coated film.
A solution to these problems is to use reactive surfactants. These have the ability to attach themselves to the latex particles irreversibly, through a covalent chemical bond.
Catalytic chain transfer polymerization (CCTP), a free radical polymerization processs that employs a cobalt catalyst in tiny amounts, is able to make polymer molecules with a reactive unsaturated end group. These macromolecules, also called macromonomers, can be chain extended using a process referred to as RAFT (Reversible Addition Fragmentation chain Transfer), into longer polymer molecules that can behave like surfactant molecules. The reactive end group is preserved, which means that if our polymer reactive surfactant is used in an emulsion polymerization to make latex particles, it will be attached permanently to the latex particles.
The technology to fabricate blockcopolymers under emulsion polymerization conditions using CCTP derived macromonomers, was originally reported in the 1990s by Moad and coworkers. Emphasis has been lying on polymer chain growth and hence the molecular weight distribution.
In our paper published in a special polymer colloids issue of the ACS journal Biomacromolecules PhD students Wai Hin Lee and Joshua Booth investigated the emulsion polymerization processes from a different angle. We investigated the particle size distributions and studied how these developed throughout a three-stage emulsion polymerization process (see the image below).
Three stages of emulsion polymerizations: Catalytic chain transfer emulsion polymerization to make an alkali soluble macromonomer, chain extension to make a reactive block copolymer surfactant, emulsion polymerization to prepare soft polymer colloids using the reactive surfactant.
Firstly, we looked at the catalytic chain transfer emulsion polymerization to make the hydrophilic block of the reactive polymer surfactants. Next we looked at how the particle size distributions changed upon chain extension with a hydrophobic block. Finally, we disintegrated the latex particles into a reactive polymer surfactant micellar dispersion. This was then used to carry out emulsion polymerizations to produce polymer latexes in absence of conventional surfactants.
Prof. dr. ir. Stefan Bon says: “I hope that people like the angle we took in our work, to shine a light on how the latex particles are formed and how the particle size distributions develop. We showed that it was possible to make soft polymer latexes with average particle diameters below 100 nm using our reactive surfactants, easily up to overall solids content of 30wt%. This is an excellent achievement. We believe that the reported emulsion polymerization processes are robust and versatile, and are delighted that we can produce polymer latexes that do not suffer from surfactant migration upon application.”
Details on the paper : https://pubs.acs.org/doi/10.1021/acs.biomac.0c00766